How 3D Printing is Changing the Boating Industry
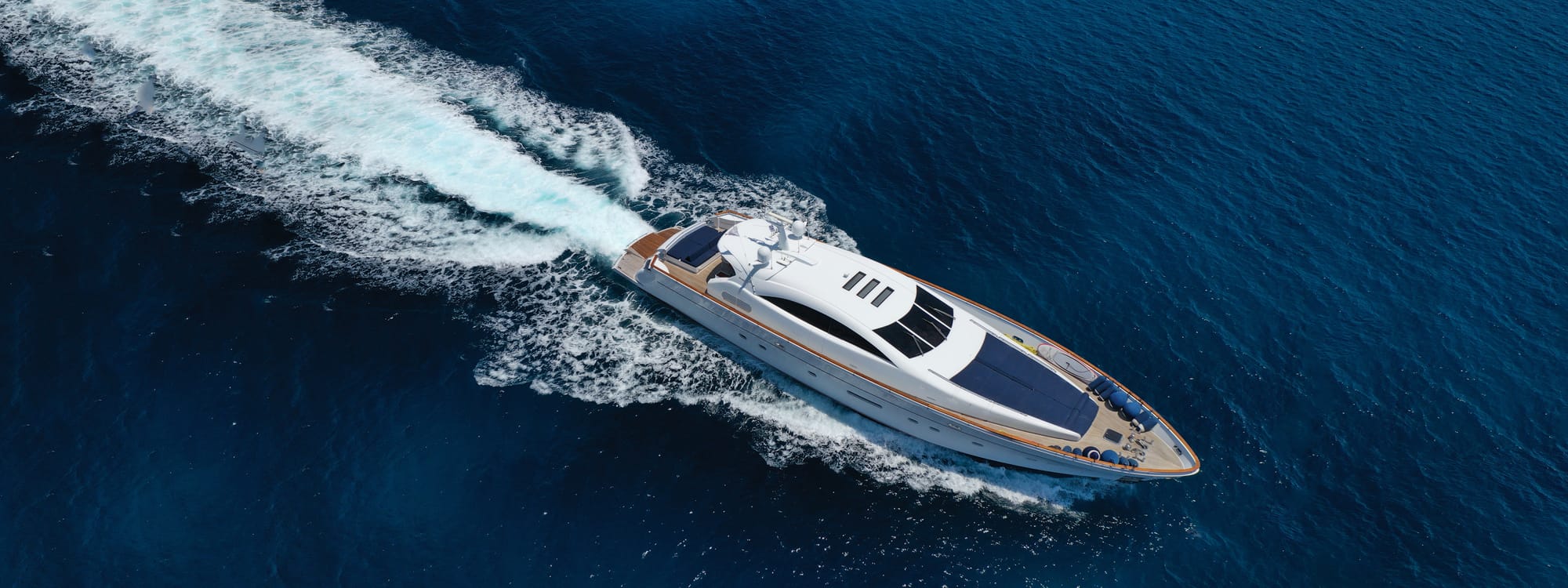
A printer is probably the last thing you would think about when it comes to building ships and boats, but with the rapid growth of 3D printing, this technology is becoming more commonplace in the boat manufacturing industry.
We’ve seen this take place already in other industries such as space, robotics, and healthcare. While the boating industry has been relatively slow to adopt this type of innovation compared to these industries, Naval architect Greg Marshall predicts that by the year 2030, entire yachts will be 3D printed. This might seem quite far off, but the boating industry has made great strides in recent years. In 2019, engineers at the University of Maine acquired the world’s largest polymer 3D printer and used it to create the world’s first and largest 3D printed boat. Even more impressive, the 25-foot, 5,000-pound boat named 3Dirigo was tested in an indoor wave pool and scored remarkably well.
So, while entire 3D-printed fleets are not feasible in 2022, we expect to see incredible advances in boat manufacturing in the near future thanks to the work of researchers and engineers around the world. In this article, we will examine how boat manufacturers are utilizing 3D printing technology, and what this means for the future of the boating and shipping industry.

Benefits of 3D Printing
When compared to conventional manufacturing processes such as subtractive manufacturing or injection molding, 3D printing offers numerous benefits that speed up production, eliminate waste, and more. Here are a few advantages of utilizing 3D printing technology:
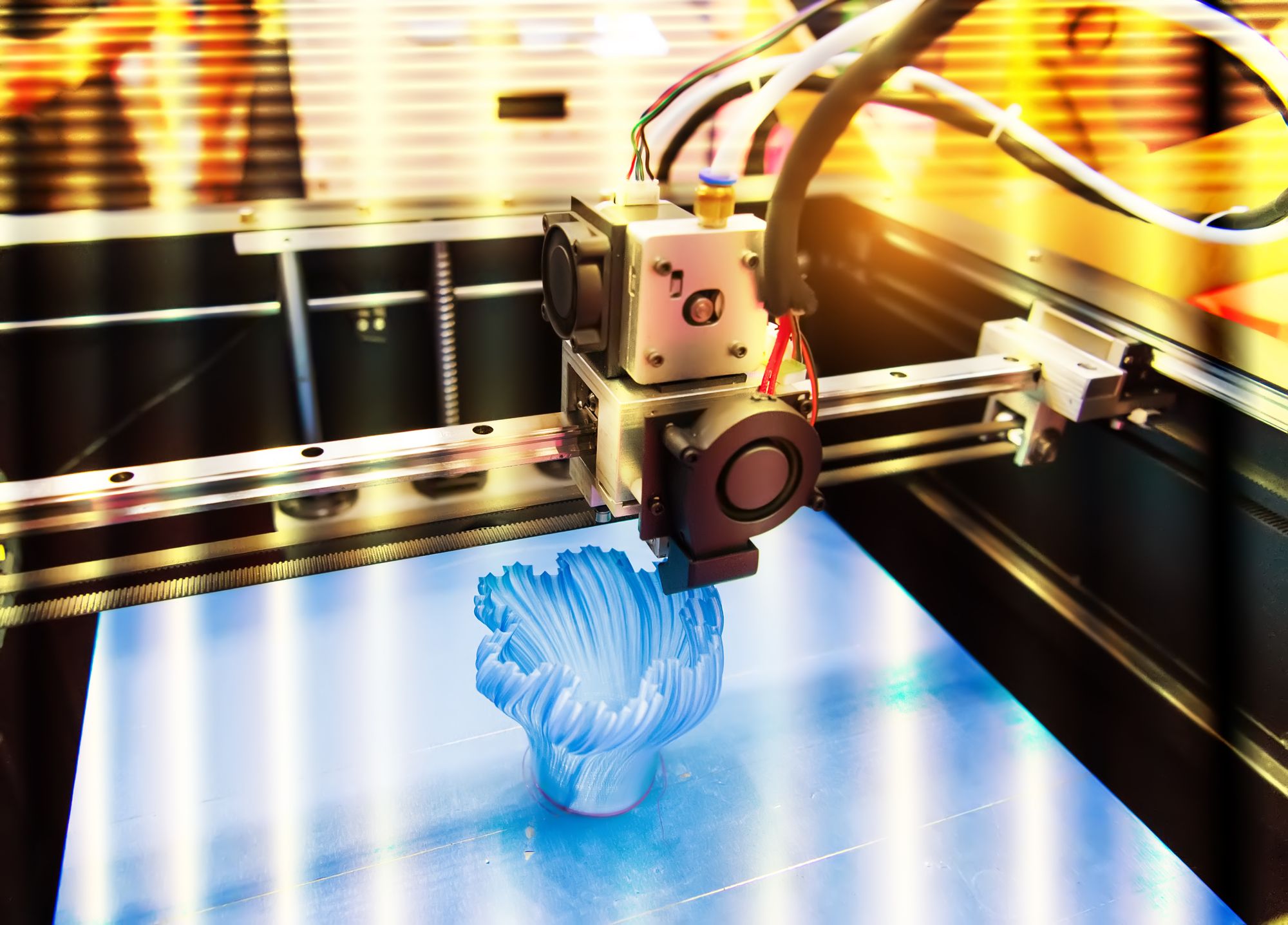
Faster Production
3D printing is considerably faster than traditional manufacturing and provides flexible production that can be ramped up and down as needed. By using this technology, boat and ship manufacturers are able to print spare parts on demand and completely bypass sourcing and procurement. Chad Mirkin, a chemist at Northwestern University, has created a high-speed 3D printer that can produce a plastic object the size of a human in just a few hours. Of course, boats are not made from plastic alone, but inventions like Mirkin’s are rapidly changing the manufacturing industry. In fact, 3D Insider states that “large-scale metal 3D printing is perceived to have the potential for the largest commercial growth with an estimated value of $739 million by 2026.”
Cost-effectiveness
Another reason 3D printing is becoming common practice for manufacturing companies is its cost-effectiveness. 3D printing requires fewer tools than traditional methods. There is no need for molds or other materials usually needed to produce a product. 3D printing only requires a printing machine and the filament used to print the designs.
Additionally, it is much easier to identify and correct mistakes early on in the printing process. When a mistake is made during traditional manufacturing, a complete do-over is often required. This can be extremely costly and time-consuming. With 3D printing, the designs are printed in layers, allowing mistakes to be spotted right away. The printer can be quickly shut off, adjustments made, and then it’s back to business without losing much time, money, or materials. And this brings us right to our next point: less materials waste.
Less Materials Waste
Traditional subtractive manufacturing begins with a massive chunk of materials that are hacked away until the desired product is created, and the leftover materials are usually discarded. 3D printing, on the other hand, is an additive process that builds the product layer by layer, only using the materials that are needed.
With 3D printing, most of the design process is done on a computer. This allows AI to produce simulations that pinpoint areas that might fail, all before printing has even started. As a result, fewer mistakes are made and less material is wasted.
Better Quality
Manufacturers can go through more design and review cycles because mistakes are caught early on and prototypes are produced much faster. This results in better design and enhanced quality. Ultimately, there is less guesswork with 3D printing than with traditional manufacturing methods. Once you have perfected the prototype, high-quality products can be produced with fewer human errors. Furthermore, every product that is printed will be identical to the prototype as long as no changes were made to the CAD (Computer-Aided Design) models.
Customization
Another selling point for 3D printers is the creativity they unlock. Older manufacturing methods limit you to the designs that the molds support, and customizations are challenging and expensive. With 3D printing, no geometrical shape is impossible, and the potential for personalization is endless. As 3D technology advances, manufacturers and individuals alike will be able to quickly design and build custom boats and accessories.
Customizable products have become a necessity for companies to stay relevant in their industry. Boat and ship manufacturers that utilize 3D printers can expect to see an increase in sales and customer satisfaction as a result of the personalization that 3D printers allow.

Looking Ahead
3D printers have massive potential in the boat and shipbuilding industry. As this technology advances and becomes more accessible to manufacturers, you can expect to see more creativity, innovation, and opportunities for growth within the industry. The speed at which spare parts alone can be produced will be a game changer for manufacturers, as well as private boat owners.
Companies will be able to produce high-quality boats in a fraction of the time that traditional processes take, and allow buyers to make customizations without completely disrupting the production process.
There’s no denying the numerous ways that 3D printers have changed manufacturing. Engineers have found a faster way of building entire boats that is more economical, sustainable, and creative, and the continuing advancement of 3D printing technology will be exciting to follow.